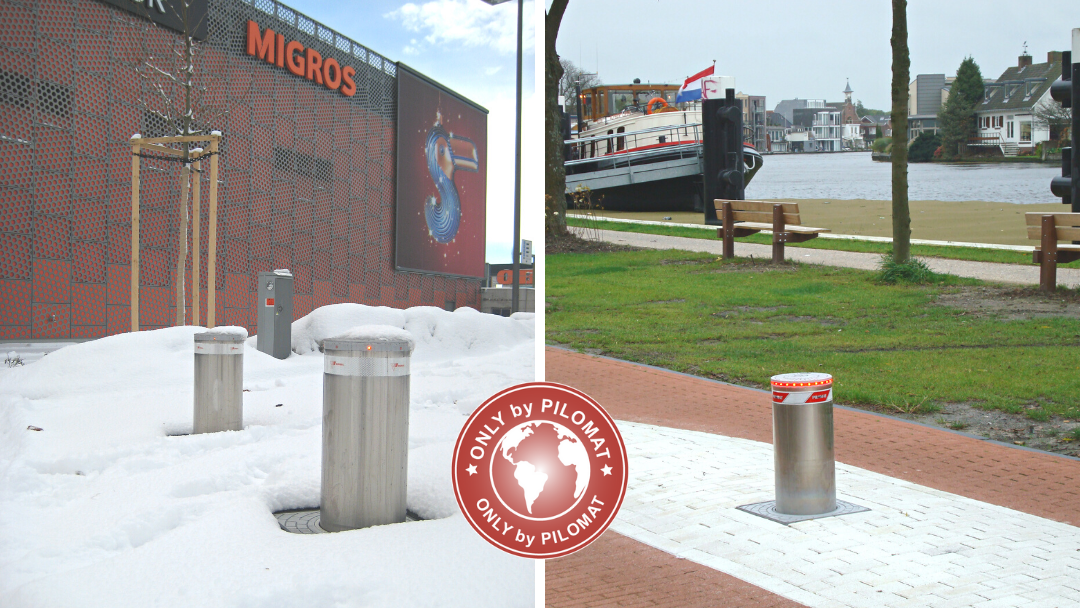
25 Jul ANTICORROSION MARINE TREATMENT
What’s the bitter enemy of our products?
If you’re planning to install a bollard or road blocker close to the sea, in a saline ambient or in cold Countries, you should read this article!
The great enemy of steel is corrosion and therefore rust. For this reason protecting steel from rust is essential: it allows the structure to operate for the entire expected life cycle; in addition, it preserves the raw material, which can be recycled at the end of the life cycle without losing even a gram in rust.
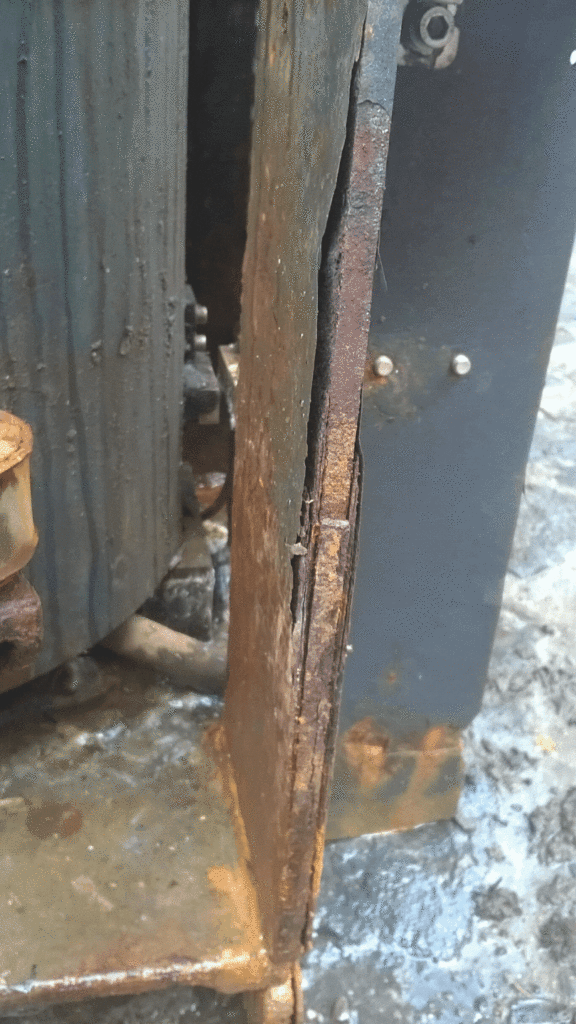
Over the years we have developed a special anticorrosion treatment, carefully studied together with our supplier, to withstand salt spray tests in the worst conditions, according to ISO 9227 standard. The anticorrosion marine treatment, a multi-stage painting process, is applicable on our range of products from bollards to road blockers, as optional. It can be applied both on the frame and the cylinder of traffic bollards, as well as on road blockers and tyre killers.
We suggest it for projects at less than 3Km from the sea or in saline ambient conditions (i.e. the presence of salt on roads to prevent ice formation).
Choose the anticorrosion marine treatment for your projects if you’re looking for the highest level of protection against corrosion, available only by Pilomat!
Why choosing our marine treatment instead of hot dip galvanizing?
Pilomat marine treatment
– Concerning the resistance to corrosion, our treatment has successfully passed the salt spray chamber test (ISO 9227) at the C5-M level for 875 hours.
– Our marine treatment allows for a final coating in the RAL decided by the customer.
– The coating finish is uniform.
– The perfect execution of the different steps ensures a long life to coating.
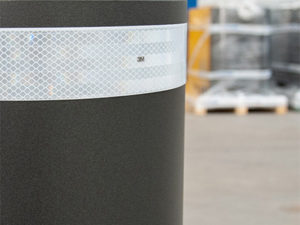
Hot dip galvanizing
– Also the hot dip galvanizing has successfully passed the salt spray chamber test according to ISO 9227.
– Applying a final coating is not possible.
– The finish of this treatment is not uniform.
– Over time it loses its initial brilliance and takes on a matte finish.
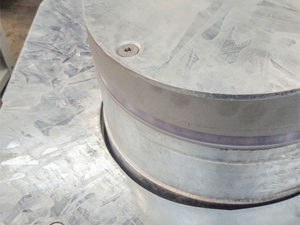
Want to know more about our standard anti-corrosion treatments?
As standard we apply a specific anti-corrosion treatment depending on the material of the product, which ensures a higher resistance of the material to corrosion and a long-lasting painting. All our treatments are made in compliance with the ISO 12944 standard, a regulation that evaluates the quality of the paint treatment depending on the level of protection to corrosion. This treatment has successfully passed the salt spray chamber test (ISO 9227) at C4 level for 740 hours.
An accurate execution is essential for the proper fixing of the final coating. Moreover the first steps, such as sandblasting and primer coating, are the ones that allow for the correct fastening of the paint to the material.